Overview
Plastic injection molding is a widely used manufacturing process for creating plastic products with complex designs. The process includes injecting molten plastic into a mold cavity, then allowing it to cool and solidify into the desired shape.The injection molding machine comprises two main components, the injection unit and the clamping unit, which work together to produce the plastic parts.
The plastic injection units are responsible for melting and placing the material into the mold. It consists of a hopper, a heater, and a screw that moves the material forward. Here, it is crucial to maintain a balanced mold to ensure the even distribution of molten plastic, preventing defects such as warping or shrinkage.
The plastic injection mold comprises several parts: the cavity, core, ejector pins, guide pillar, and clamp plate. The cavity and core create the shape of the plastic part, while the ejector pins push the finished part out of the mold. The guide pillar and clamp plate hold the mold in place during production.
In summary, plastic injection molding is an ideal choice for high-volume production of plastic components. With the help of an effective injection unit and well-designed molds, it’s possible to create high-quality plastic products quickly and efficiently.
Some Key Facts About Plastic Injection Molding
1. According to a report by Grand View Research, the global plastic injection molding market size was valued at USD 265.1 billion in 2019 and is expected to grow at a compound annual growth rate (CAGR) of 5.0% from 2020 to 2027.
2. The automotive industry is the largest end-use industry for plastic injection molding, accounting for over 30% of the market share. Other major end-use industries include packaging, healthcare, and electronics.
3. Injection molding is the most commonly used manufacturing process for producing plastic products, accounting for 36% of all plastics processing in the United States.
4. The Asia-Pacific region is the largest market for plastic injection molding, with China being the largest contributor to the market share due to its large manufacturing industry.
5. The use of biodegradable and eco-friendly raw materials in plastic injection molding is rising, with a growing demand for sustainable products and packaging solutions.
6. The global market for plastic injection molding machines is also expected to grow, with a CAGR of 4.6% from 2020 to 2025, driven by the increasing demand for plastic products and the development of advanced technologies in the industry.
7. According to a report by Mordor Intelligence, the medical sector is expected to be the fastest-growing end-use industry for plastic injection molding, with a CAGR of 6.3% from 2020 to 2025, driven by the increasing demand for medical devices and equipment.
Benefits of Plastic Injection Molding
Plastic injection molding offers numerous benefits, making it the ideal choice for the mass production of identical plastic products. Its cost-efficient and easy production process utilizes CNC machines that produce high-quality plastic components in a fraction of the time compared to traditional manufacturing methods.
This technique has changed the face of the plastic industry, offering a range of customization options that were once impossible to achieve with other manufacturing processes. Whether you need complex designs or simple parts, plastic injection molding can handle your every requirement.
You can quickly reach a high-volume production rate with injection molding, meeting tight deadlines and reducing manufacturing initial costs. This technology can easily produce large orders of identical parts, ensuring consistency throughout your production runs.
Overall, the benefits of plastic injection molding are clear. Its efficiency, versatility, and cost-effectiveness make it the preferred manufacturing process for various industries. Whether you’re in the automotive industry, medical industry, or producing consumer products – plastic injection molding is the way to go.
Key Benefits
1. Plastic injection molding is an efficient manufacturing process that produces high-quality products quickly and accurately.
2. The versatility of plastic injection molding allows for a wide range of shapes, sizes, and materials to be used, making it ideal for many industries.
3. The cost-effectiveness of plastic injection molding makes it a preferred choice for manufacturers looking to produce large quantities of products at a low cost per unit.
4. The ability to precisely create complex shapes and intricate details makes plastic injection molding popular for automotive, medical, and consumer products industries.
5. Plastic injection molding allows for using recycled materials, making it an environmentally friendly option for manufacturers.
6. The durability and strength of plastic injection molded products make them ideal for a
7. The consistency and repeatability of plastic injection molding ensure that each product is of the same high quality, reducing the risk of defects and improving customer satisfaction.
8. Overall, the benefits of plastic injection molding make it the preferred manufacturing process for a wide range of industries, offering efficiency, versatility, and cost-effectiveness.
The Process Involves Several Critical Steps.
The plastic injection molding process is a complex and intricate technology that involves a series of critical steps. It requires excellent knowledge of manufacturing technology, manufacturing methods, and many other factors to achieve the perfect product. To produce the desired plastic component, it is essential to understand the critical steps involved in the entire process. Here’s a comprehensive guide to the critical steps in the plastic injection molding process, helping you understand the techniques and technologies required to create perfect plastic parts.
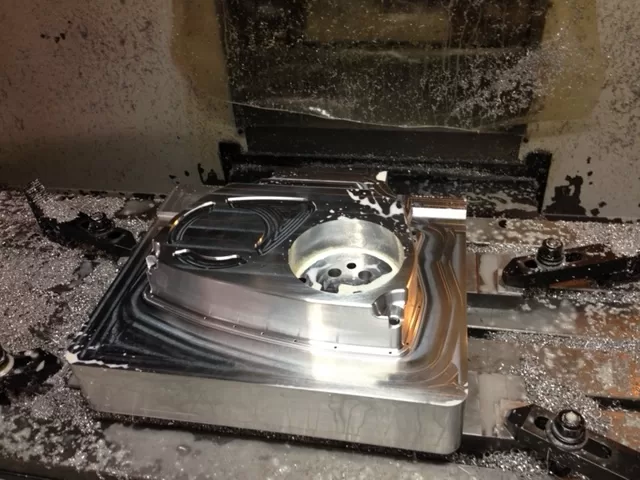
1. Clamping the Mold
Clamping the mold is a vital step during the injection molding process. This involves securing the two halves of the mold together using a powerful hydraulic system. Sufficient clamping pressure is critical to prevent leaks and flashing defects, which can significantly impact the quality of the plastic part being produced.
Leakages can occur when molten plastic oozes out of the mold cavity due to inadequate clamping force. On the other hand, flashing defects happen when excess molten plastic escapes from the mold and forms a thin layer around the edges of the plastic part.
Choosing the right type of mold can also play a significant role in the injection molding process. Conventional molds are typically used for simple shapes, while stack molds can be used for more complex designs. Hot runner molds are ideal for high-volume production runs, providing faster and more efficient cycles.
In summary, ensuring sufficient clamping pressure during injection molding is crucial in producing high-quality plastic parts while selecting the appropriate mold can help optimize the manufacturing process.
2. Injecting the Molten Plastic
The injection unit takes over after completing the clamping step in the injection molding process. The injection unit is responsible for melting the pellet-shaped plastics and injecting the resulting liquid plastic into the mold cavity. The pellets are loaded into a hopper and then fed into the injection unit.
The injection unit consists of a screw that plasticizes the pellets and a barrel where this plasticizing occurs. Once the plastic is injected into the mold cavity using an injection molding press, the pressure and temperature of the molten plastic are crucial in ensuring the final product’s quality.
The holding phase starts after the plastic has been injected into the cavity. During this phase, the plastic is held in the cavity under a certain pressure level to ensure proper filling and prevent sink marks. This phase is followed by the cooling phase, where cooling channels within the mold help cool the plastic and solidify it.
The injection molding process depends heavily on properly controlling temperature, pressure, and cooling to produce high-quality and consistent products. An injection molding press and techniques like cooling channels enable the holding and cooling phase to occur properly and ensure the final product’s quality.
3. Holding and Cooling
Once the molten plastic has been injected into the mold cavity during plastic injection molding, the holding phase begins. This phase is crucial as it ensures proper cavity filling and prevents sink marks in the final product. The holding phase involves holding the plastic in the cavity under a certain amount of pressure until it cools and solidifies to a specific level. The exact duration of the holding phase depends on the plastic material used, the size and shape of the product, and the injection pressure.
Cooling channels within the mold play a critical role in the cooling phase of plastic injection molding. These channels assist in rapidly dissipating heat from the plastic and cooling it down so it solidifies quickly and accurately. The cooling agents used are usually water or oil, depending on the intended use of the final product.
Sink marks can occur if the plastic cools too quickly or unevenly, leading to depressions in the final product’s surface. Causes of sink marks include inadequate holding pressure, incorrect holding time, or insufficient cooling channel design. Properly holding and cooling the molten plastic during the injection molding process can prevent sink marks and ensure the final product’s quality.
4. Selecting the Material and Design Stage
Selecting the right material and designing the mold is crucial for successful plastic injection molding. During the material selection process, it is important to consider various factors that will impact the final product’s performance, such as strength, durability, flexibility, temperature resistance, chemical resistance, and cost.
Materials commonly used in injection molding include thermoplastic, thermoset, and elastomers. Thermoplastics are adaptable and have a high melting point, making them suitable for products that require high strength and durability. On the other hand, thermosets are ideal for chemical-resistant products due to their exceptional hardness and rigidity. Elastomers are flexible materials suitable for products that require high elasticity.
CAD software plays an essential role in the design stage and enables visualizing the product and testing of different scenarios to make necessary modifications before mold development. Even minor design changes can increase tooling costs; therefore, it is critical to prioritize and review the design and material selection before finalizing mold development.
In conclusion, the material selection and design stage are fundamental in plastic injection molding and require careful consideration of the product’s requirements to select the best material and design for successful production and minimize tooling costs.
5. Ejection of the Molded Parts
Once the molten plastic has been injected into the mold and sufficient time has been allowed for its cooling, the ejection process can begin. The ejection mechanism then separates the now-solid molded part from the mold cavity, which can be achieved either through a mechanical or hydraulic system. A complex mold may require multiple ejection points to ensure that the part releases from the mold uniformly.
After ejection, a flash of excess material called gate vestige typically must be removed. This process involves trimming the excess material from the molded part using specially designed equipment. Waste material removal represents another crucial aspect of the injection molding process, to minimize scrap and for efficient recycling.
Manufacturers must ensure that the entire molding process is carefully monitored for achieving a consistent and reliable manufacturing solution. The injection pressure, plastic temperature, and cooling water parameters must be finely tuned to prevent any variations in the characteristics of the finished molded part. Real-time monitoring using sensors and software analytics offer an efficient and reliable automated solution. A robust mold-ejection and waste-removal system and comprehensive monitoring can improve production economy and product quality.
Types of Injection Molding
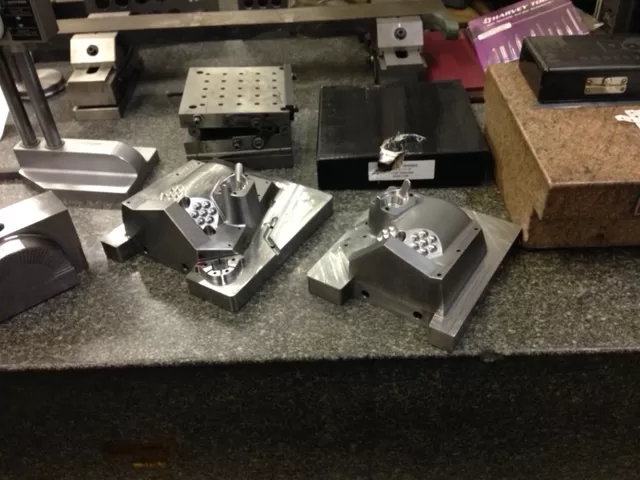
Injection molding is a widely used manufacturing process for producing a wide range of plastic products used in various industries like automotive, medical, and consumer goods. One critical factor in this process is the injection mold, which shapes the molten plastic into a specific configuration. Various types of injection molds are used in manufacturing, depending on the complexity of the design, production volume, and material type.
Vertical Plastic Injection Molding
Vertical Plastic Injection Molding is an injection molding process where the injection mechanism is positioned at the top of the mold. This allows gravity to fill the mold cavities, leading to quicker filling time and a consistent flow of molten plastic during the injection. Unlike traditional horizontal injection molding, this method utilizes the vertical axis of the machine to achieve greater precision and efficiency.
One of the key features of a vertical injection molding machine is the presence of rotary blades that allow the machine to operate with multiple concurrent processes during one cycle. This results in higher productivity, increased efficiency, and less manual intervention. Additionally, the open clamps of the machine make it easier for the operator to load and unload the mold, providing improved ergonomics and a safer working environment.
Overall, Vertical Plastic Injection Molding is an ideal choice for high-volume production of plastic components. With the ability to work with a wide range of plastic materials, this manufacturing process is widely used in the automotive and medical industries to produce various consumer products. Compared to traditional horizontal injection molding, the vertical method offers faster cycle times, reduced production costs, and improved product quality.
Horizontal Plastic Injection Molding
Horizontal plastic injection molding is a manufacturing process that involves injecting molten plastic into a mold cavity. The molding machine is oriented horizontally, and the molten plastic is injected into the mold cavity using high pressure. The machine’s horizontal axis allows easy access to the mold, making it easier to operate and maintain.
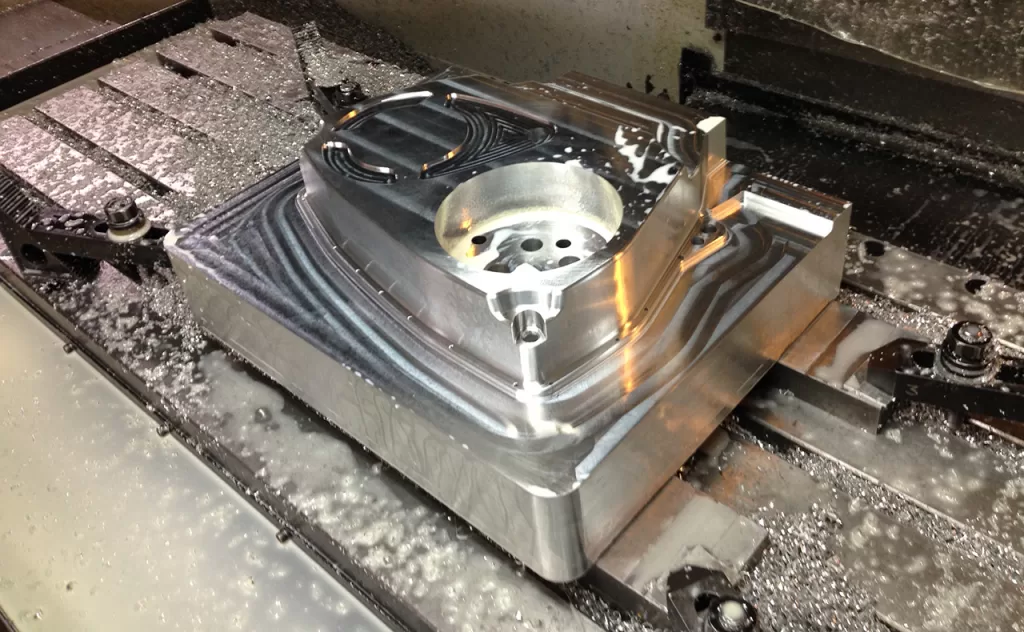
One of the benefits of horizontal injection molding is automatic part ejection without manual extraction. After the molding cycle is completed, the part is automatically ejected from the mold, eliminating the need for manual intervention. This saves time and reduces labor costs, making horizontal molding ideal for high-volume production runs.
Another feature that makes horizontal molding attractive is the ability to produce more plastic parts per cycle. The horizontal orientation allows for extra cavities, which increases production capacity. This makes horizontal molding an ideal choice for projects that require mass production of plastic products, such as the automotive and medical industries.
Multi-cavity molds are another option for horizontal injection molding. These molds have multiple cavities, allowing for producing even more plastic parts in a single cycle. The cost of multi-cavity molds is higher than a single-cavity mold, but the higher production volume per cycle can result in lower manufacturing costs overall.
Open-faced Molds
Open-faced molds are a type of injection mold used in manufacturing plastic products. As the name suggests, these molds have an open face that allows the molten plastic to flow into the space between the mold’s cavity and the parting line. This makes the mold cavity easily accessible, increasing production speed and reducing production costs.
Open-faced molds are ideal for producing plastic components that have a relatively simple design. This type of mold does not require complex designs, which means that it can be used to produce a wide range of plastic products, including consumer products, automotive parts, and medical devices.
Another advantage of open-faced molds is that they are relatively easy to manufacture. The mold cavity is made by machining or cutting out a block of steel or aluminum to the desired shape and size. After mounting the mold onto an injection molding machine, the molten plastic is injected into the mold cavity with high pressure.
Open-faced molds are also an ideal choice for high-volume production runs. They allow for mass production of plastic parts at a very high production rate, which makes them perfect for manufacturing large quantities of plastic parts quickly and efficiently.
One of the disadvantages of open-faced molds is that they do not allow for the production of complex designs. The mold cavity cannot have any undercuts or overhangs, limiting the types of plastic parts that can be produced using this mold. A closed or hybrid mold may be necessary for more complex designs.
In conclusion, open-faced molds are an excellent choice for producing plastic parts with a relatively simple design. They are easy to manufacture, allow for high-volume production, and are cost-effective. If you are looking for an efficient and reliable manufacturing technology for your plastic injection molding project, open-faced molds might be the perfect choice for you.
Two-piece Molds
Two-piece molds are a common design used in plastic injection molding. This type of mold consists of two halves that are joined together to enclose the mold cavity. The two halves can be easily separated to remove the molded part, resulting in reduced production time.
The mold design for a two-piece mold is relatively simple but is determined by the shape of the molded part. The two halves of the mold are identical and fit together perfectly, creating a seal that prevents the molten plastic from leaking out.
The mold cavity is created by machining or cutting out the desired shape and size of the part and then splitting it into two halves. The two halves of the mold are then mounted onto an injection molding machine, and the molten plastic is injected into the mold cavity at high pressure.
After the plastic has solidified, the two halves of the mold are separated, and the molded part is removed. This design allows for faster and more efficient production of plastic components, especially when compared to open-faced molds.
Overall, two-piece molds are a versatile and efficient choice in plastic injection molding. Their design, ease of use, and quick production time make them a popular manufacturer choice.
Three-piece Molds
Three-piece molds are a type of mold used in plastic injection molding. Unlike two-piece molds, three-piece molds include an additional component that separates the two halves of the mold, allowing for easier removal of the molded part.
The design of three-piece molds typically involves a core, cavity, and stripper plate. The core and cavity create the desired shape of the part, while the stripper plate helps to eject the part from the mold. This design allows for more intricate shapes and designs to be created, as the part can be ejected without damaging any fragile details.
The function of three-piece molds also differs from other types of molds. The use of a stripper plate allows for the molded part to be removed without the need for excessive force, preventing damage and reducing downtime. Additionally, using a three-piece mold can improve production efficiency, as the molded parts can be ejected, and the mold can be quickly set up for the next production run.
In summary, the advantages of using three-piece molds in the plastic injection molding process include the ability to create complex designs, easier part ejection, and improved production efficiency.
Multi-cavity Molds
Multi-cavity molds are injection molds designed to produce multiple parts of the same design in one production cycle. These molds are ideal for projects where economies of scale are important, as they can help save on production costs. While multi-cavity molds are often more complex and require higher tonnage machines, their ability to produce large volumes of parts at once can ultimately lead to significant cost savings.
The number of cavities in a multi-cavity mold can vary depending on the size of the part and the production volumes required. A mold may contain up to 128 cavities for smaller parts, while larger parts may have as few as four cavities. Despite the added complexity of multi-cavity molds, they are still widely used in manufacturing industries where high-volume production runs are needed.
While multi-cavity molds may require a higher initial investment in tooling and machinery, they offer significant cost savings in the long run by streamlining production processes and allowing for larger production volumes. Companies looking to produce thousands or even hundreds of thousands of parts should consider multi-cavity molds as an ideal choice for their manufacturing projects.
Stackable Molds
Stackable molds are a specialized type of Injection Mold consisting of more than one layer, providing a considerable increase in productivity. By adding more and more layers, stackable molds can produce several times the yields in a single molding process, saving both time and costs. Using stackable molds, manufacturers can achieve great speed and efficiency, sometimes raising productivity to four times that of regular molds.
The main benefit comes from using multiple layers, each capable of producing separate parts simultaneously in a single molding cycle. This means that manufacturers can produce a higher volume of parts, while also reducing the number of molds required, resulting in lower tooling costs. In addition, stackable molds significantly reduce production time, allowing manufacturers to bring their products to the market faster.
Overall, Stackable Molds can be an ideal choice for manufacturers in various industries requiring high-volume production and precision. It is an effective solution for complex designs, delivering consistent quality for large-scale plastic part production.
Overmolding vs. Insert Injection Molding
Overmolding and insert injection molding are two plastic injection molding processes that involve using multiple materials to produce a finished product. Overmolding, which is also known as two-shot molding, involves the injection of one material into a mold, followed by a second material directly over it. On the other hand, injection molding involves inserting a pre-formed component into a mold before it is filled with molten plastic. Let’s explore the differences between the two processes, their advantages, and when each is best suited for a particular application.
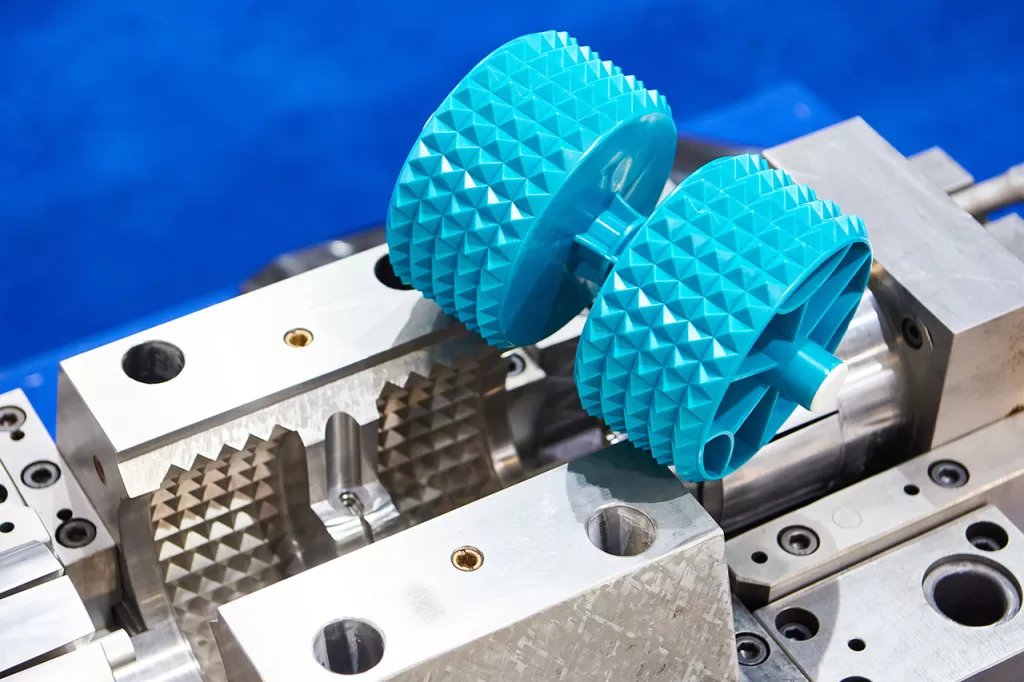
Overmolding
Over molding is a manufacturing process in which two different materials are combined to create a single new product. This process allows for multi-component pieces, and the four most common types include plastic over plastic, rubber over plastic, plastic over metal, and rubber over metal.
One of the major advantages of over-molding is its extensive flexibility with materials and construction. The core piece does not need to be injection molded, allowing for a wide range of materials to be used, including thermoplastics and metal components. This provides a cost-effective option to produce complex designs and plastic components with varying textures and properties. With over-molding, more design freedom is provided since designers can choose different materials for specific regions suited to different environments, applications, and uses.
In summary, over-molding is an ideal choice for high-volume production, and it enables manufacturers to deliver an optimal product that meets the specific needs of the consumer product, medical, and automotive industries, among others, with excellent finishing, aesthetics, and functionality.
Insert Injection Molding
Insert Injection Molding is an advanced technique that offers numerous advantages over traditional Overmolding. Overmolding requires the core piece to be injection molded, limiting the material options and design freedom. On the contrary, Insert Injection Molding allows for inserts to be placed into the mold cavity before injecting melted plastic, providing more design flexibility.
However, the inserts require a protective design to avoid dislodging during the process. The inserts must be held tightly in place to ensure proper positioning and avoid compromising the quality of the final product.
One of the most significant advantages of Insert Injection Molding is reduced assembly costs since parts can be formed simultaneously. The technique also reduces material waste and improves design strength, making it an ideal choice for the mass production of complex plastic components.
Moreover, Insert Injection Molding is vital in the medical device industry, where precision and accuracy are of utmost importance. The method allows for the integration of various materials to create complex geometries that meet the end-user’s specific needs while enhancing the medical device’s overall performance.
In summary, Insert Injection Molding offers exceptional design flexibility, reduced assembly costs, material waste reduction, and improved design strength, and is a game-changer for medical device production.
Cleanroom Molding
Cleanroom Molding is a method that utilizes a specially designed room to minimize the chances of contamination during the production of plastic parts. The procedure is conducted in a controlled environment with strict regulation of air quality and particle count. The cleanroom is equipped with HEPA filters that prevent dust and other contaminants from entering the room.
The different classes of cleanrooms are classified according to their level of cleanliness. These classes range from Class 1 to Class 9, with Class 1 being the most stringent. Cleanroom molding is particularly important in the pharmaceutical and medical industries, where the risk of contamination can have severe consequences.
Mold tooling is a crucial aspect of the mold-making task, and its success is directly linked to precision analysis. Gate sizing is an essential part of mold tooling that determines the right size of the gate to inject the molten plastic into the mold. A poorly-sized gate can result in defects during the molding process. Regular tooling maintenance is also necessary for injection molding to ensure it is in good condition and ready for use.
In conclusion, Cleanroom Molding, Class 1-9 cleanrooms, and mold tooling are essential for mass production of plastic parts in pharmaceutical and medical industries. The precision analysis of gate sizing and proper maintenance of tooling can make a significant difference in the success of the injection molding process.
3. Mechanical Fastening
Mechanical fastening is essential in injection molding, and several options are available when designing molded parts. Threaded fasteners, for example, provide a strong mechanical bond between two parts, while undercuts allow molded parts with complex geometries to be mechanically fastened.
Designers of molded parts have three options: designing a thread directly on the part, adding a boss, or including a threaded insert. Designing a thread directly on the part is a cost-effective way of including threads, but it leads to low strength and potential stripping. Adding a boss, however, can provide the needed strength and allow for a more significant load-bearing area. Including a threaded insert provides excellent strength and allows for easy replacement in case of damage.
After designing the mold, the finishing and assembling process is a crucial element in ensuring the mold is in good condition and ready for use. Mold assembly includes placing the printed mold inside a standard metal frame or a Master Unit Die. This process ensures that the mold is held in position and performs better during injection molding.
Plastic Injection Molding Post-Processing Operations
Plastic injection molding is a widely used manufacturing process that involves melting plastic pellets and injecting them into a mold cavity. The molten plastic then cools and solidifies, resulting in a plastic part. However, the process doesn’t stop there. To achieve the desired finish and functionality of the part, there are post-processing operations that must be performed. From removing the molded parts from the mold to finishing and decorating them, post-processing operations play a critical role in the plastic injection molding process. In this article, we’ll guide you through everything you need to know about post-processing operations in plastic injection molding.
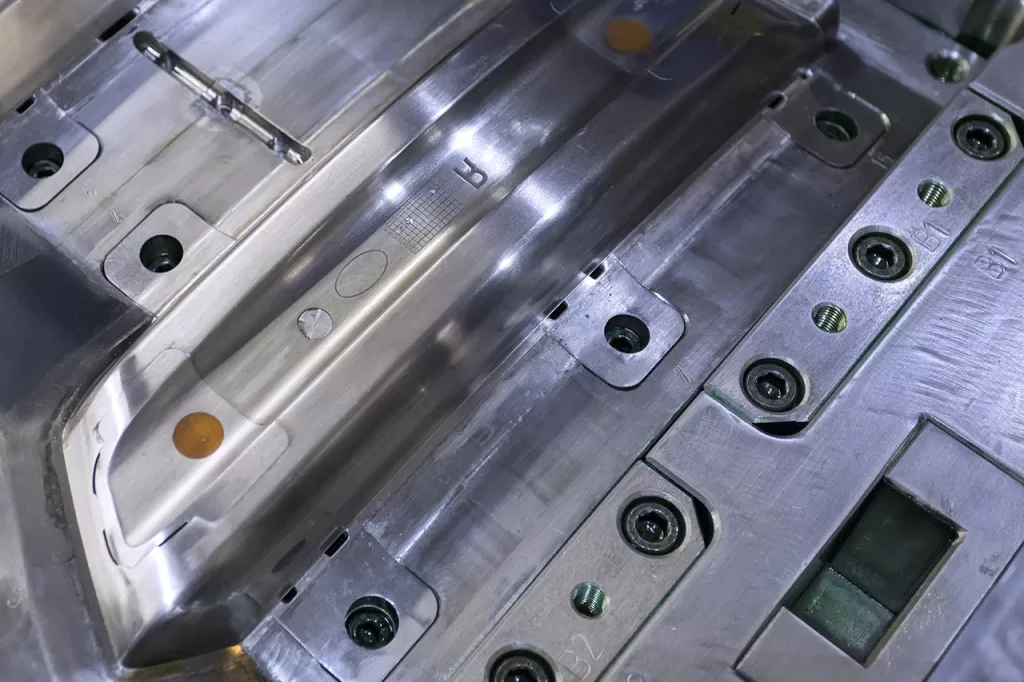
Part Decoration
Part decoration is a crucial factor in injection molding design, and it involves several techniques to enhance the appearance and functionality of plastic parts. Various decoration techniques are available, such as spray painting, powder coating, silk screening, pad printing, and metal plating. Each technique has its advantages and disadvantages in terms of cost, durability, and quality.
Spray painting is a common technique for plastic part decoration due to its versatility and ease of application. On the other hand, powder coating involves electrostatically charged particles that adhere to the surface of the plastic. Silkscreening is perfect for logos or text, and it involves the transfer of ink through a mesh screen onto the injection-molded part. Pad printing is ideal for complex designs and textures, while metal plating offers excellent durability and a high-quality appearance.
Part appearance and geometry are significant factors in selecting the project’s optimal technique and resin choice. The surface finish, color, gloss, and texture requirements of the plastic part will determine the best method for decoration. Also, the part’s geometry must be considered to determine the optimal printing or plating area. Understanding these factors will help choose the most suitable technique and resin for the project.
Pad Printing
Pad printing is an ideal printing technique for plastic injection molding design due to its ability to print 2-D images onto 3-D objects. This process involves the transfer of ink onto the injection molded part using a silicone pad. First, the desired image or text is etched onto a plate, and ink is added to the etched area. Then, the silicone pad picks up the ink and transfers it onto the curved surface of the plastic part.
Silicone pads are advantageous for printing onto rigid parts with round shapes. The pads have the ability to conform to the curvature of the part, allowing for even distribution of the ink. The result is a high-quality, long-lasting print that is resistant to wear and tear. Additionally, silicone pads can print multiple colors simultaneously, making it an ideal choice for logos or multicolor designs.
Compared to other printing techniques, such as inkjet printing, pad printing is more suitable for uneven surfaces and can achieve better print quality. It also has a higher production rate, making it a practical choice for mass production.
Pad printing is a widely used printing method in plastic injection molding in the USA. Its flexibility and high-quality results make it an ideal choice for producing high quantities of plastic parts with customized designs.
Laser Techniques
Laser techniques have become increasingly popular in plastic injection molding design due to their high precision and efficiency. Laser etching and laser engraving are two types of laser techniques. Laser etching is the process of using a laser to create markings on a plastic surface. In contrast, laser engraving removes material and creates cavities on the plastic surface.
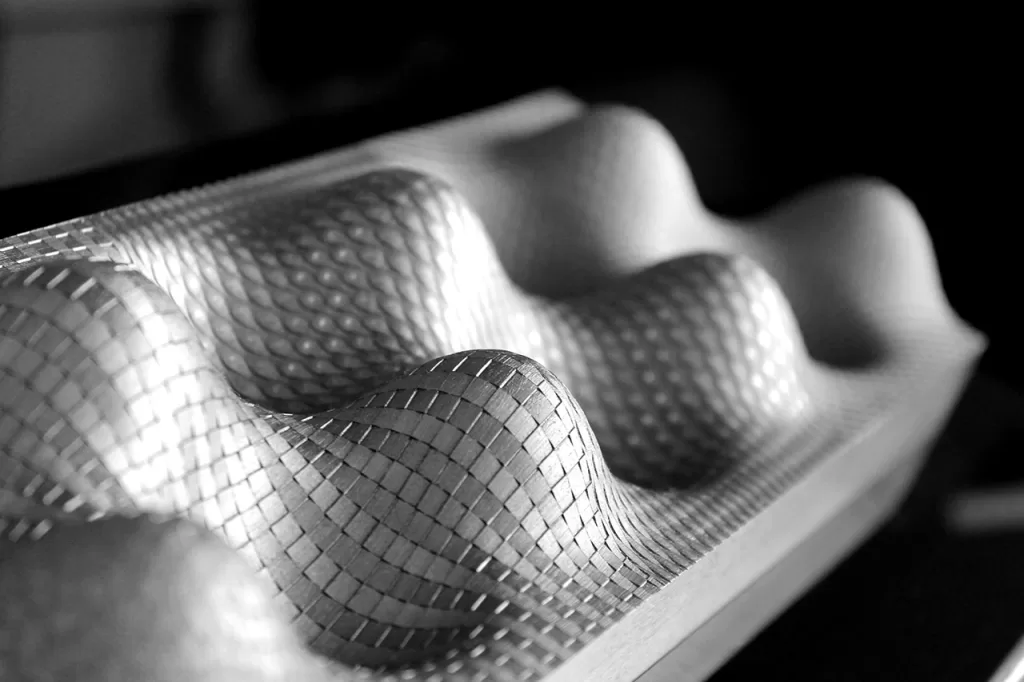
Laser etching is commonly used to create plastic parts’ product labels, logos, and barcodes. It is a non-contact process that produces high-resolution and high-contrast markings without affecting the integrity of the plastic surface. On the other hand, laser engraving is used for creating complex cavities and patterns on plastic surfaces. It is a highly precise process that can create intricate designs with fine details.
Optical molding polycarbonate is another process that is used for creating high-precision optical components from polycarbonate without the need for polishing. This process involves molding a polycarbonate replica of a polished mold insert, using the material’s refractive index to achieve the desired optical properties. The result is a high-quality, cost-effective optical component ideal for automotive, medical, and consumer product applications.
Inkjet Printing
Inkjet printing is a fast-growing technology in the plastic injection molding industry, utilized for various purposes such as marking products, adding logos or serial codes, and other forms of marking. By using inkjet printing, non-contact printing becomes possible, giving more accurate, quality results without causing any damage to the plastic surface. Unlike traditional printing methods using etching, which can sometimes leave marks, inkjet printing is a viable alternative for marking products without affecting material integrity.
The ink used in inkjet printing has unique characteristics, such as fast drying, which makes it ideal for high-speed printing machines. The ink is also heat-resistant, maintaining its color and quality even under high temperatures, which is common in injection molding processes.
Inkjet printing allows for using colored and pigmented inks, providing versatile and creative printing options for plastic parts. Colored inks provide almost photo-quality texts or images with high contrast, while pigmented inks are more vivid and attractive. Using inkjet printing also results in higher resolution and precision, translating into more precise marking and branding.
In summary, inkjet printing is a viable solution for non-contact marking in plastic injection molding, offering faster production time, versatility, and higher-quality results. Its unique characteristics, such as fast drying, heat resistance, and color variety, make it an excellent choice for printing texts or images on plastic parts.
Part Assembly
Post-molding assembly is an essential process in producing plastic parts as it determines the quality and durability of the final product. Some of the most common methods used in post-molding assembly include ultrasonic welding, adhesive bonding, and solvent bonding. Ultrasonic welding uses high-frequency vibrations to melt and fuse plastic parts together, while adhesive bonding involves using special adhesives to join parts. Solvent bonding, on the other hand, uses solvents to dissolve and fuse plastic parts together.
Manufacturers adopt the Design for Assembly (DFA) process to reduce assembly time and costs. The DFA process aims to simplify the assembly process by redesigning the product for easy assembly. It involves analyzing the product design and identifying the most efficient way of assembling the parts. This process eliminates unnecessary parts, and the product is designed with assembly in mind.
Assembling a mold for injection molding requires using a metal frame or a Master Unit Die. The frame or Die supports the mold against high pressure during the injection molding process. The mold consists of two halves, and the assembly process involves bringing the two halves together using bolts or clamps. The mold must be inspected and tested for accuracy before using it in the injection molding process.
In conclusion, post-molding assembly, Design for Assembly, and mold assembly are crucial processes in injection molding. Understanding these processes is essential to improve the final product’s quality and reduce costs.
2. UV Bonding
UV bonding is a technique used in plastic injection molding materials to bond two parts together using an adhesive that is cured by UV light. This process is ideal for applications that require a strong, durable, and visually appealing bond. Unlike traditional adhesives, UV bonding does not require heat or solvents and is, therefore, a more environmentally friendly option.
High-intensity lighting is used to dry the adhesive quickly and efficiently to ensure a successful UV bond. This reduces production time and minimizes rejection rates due to incomplete curing. The use of high-intensity lighting also ensures consistent curing throughout the bonding process, resulting in a strong and reliable bond.
Choosing the right type of resin is essential for effective UV bonding. A transparent resin that allows UV light to pass through effectively is necessary to ensure proper adhesive curing. With advancements in technology, there are now specialized resins on the market that are specifically designed for UV bonding applications.
Overall, UV bonding is ideal for those looking for a fast and efficient way to bond plastic components. It offers a more environmentally friendly option than traditional adhesives and provides a strong and reliable bond for various applications.
How to Choose an Injection Molding Partner
Injection molding is a versatile manufacturing process widely used in producing a wide range of plastic products in many industries, including automotive and medical. However, choosing the right injection molding partner is crucial to ensure the success of your project. From design to production, many considerations must be taken into account. In this guide, we will discuss some key factors you should consider when choosing an injection molding partner to help you make an informed decision.
Volume and Capacity Specialization
When choosing an injection molder, it’s important to consider the expected production volume. For low-volume manufacturing, single-cavity tooling is commonly used as it allows for more flexibility in the process. On the other hand, high-volume production can benefit from mass production, which can lower overhead costs and increase profits.
To reduce injection molding costs, reviewing the design before placing orders is recommended. This can help identify potential design flaws that may increase material costs and production time. Additionally, utilizing older molds for production runs can help reduce costs, as tooling costs can be a significant expense.
Understanding the expected volume and capacity specialization can help determine the best course of action when choosing an injection molder, and implementing cost-saving measures can help maximize profits.
Determine the Required Press Tonnage
Determining the required press tonnage for plastic injection molding is essential for efficient production. The clamping force, expressed in tons, is necessary to keep the mold securely closed during the injection molding process. Factors such as the mold surface area, part depth dimension, and melt flow must be considered to calculate the required press tonnage.
Firstly, the mold surface area, measured in square inches, is determined by multiplying the molded part’s length and width. Then, the part’s depth dimension, measured in inches, is also considered. The higher the depth dimension, the more clamping force will be required.
Secondly, the melt flow of the plastic material must also be considered. A high melt flow requires more clamping force to ensure that the melted plastic is adequately contained within the mold cavity.
Finally, press tonnage calculator tools are available online to give a close estimate of the necessary clamping force. These tools consider the mold surface area, the part depth dimension, and the plastic material’s melt flow.
In conclusion, determining the required press tonnage for plastic injection molding is crucial to avoid production delays, defective parts, and costly downtime. By considering the mold surface area, part depth dimension, and melt flow, as well as utilizing press tonnage calculator tools, the ideal clamping force can be estimated for efficient production.
Compliance to Designs
Compliance to a design is integral in achieving a high-quality plastic injection molded part. Meticulous design validation plays a crucial role in ensuring that the intended functionalities of the part are met before production. There are various methods for verifying design, ranging from physical testing to the use of simulation software.
Design validation helps to identify potential issues before production, such as potential design limitations that could affect the quality of the plastic part. One major limitation is the mold shape. If the mold’s shape is too intricate or complex, it may result in additional manufacturing costs or defects. Additionally, the wall thickness of the part must also be considered. If it is too thin or too thick, it may increase production time or lead to defects.
Ultimately, compliance to designs is essential for achieving a quality plastic part. Through meticulous design validation and consideration of potential limitations, manufacturers can ensure that the production runs smoothly while still meeting the intended functionalities of the part.
What are the expenses associated with plastic injection molding?
Plastic injection molding is a widely used manufacturing process in various industries, including automotive and medical. Before considering plastic injection molding as an option, it is essential to understand the various factors that influence the cost of the process. These factors can significantly impact the overall cost of production, from tooling and raw material to design validation and production runs. This article will discuss the significant factors that impact the cost of plastic injection molding and provide insights into reducing these costs to make it a cost-effective and efficient production method.
Different Types of Mold Materials
The mold material is crucial in injection molding, impacting the final product’s quality, production cost, and tooling life. Choosing the right steel grade for mold creation is vital to ensure the mold withstands high pressure and temperature during manufacturing.
Tool steel and aluminum are two popular mold material options. Tool steel is known for its toughness, wear resistance, and durability, making it ideal for high-volume production runs. Aluminum, on the other hand, is more cost-effective and preferred for low-volume production and prototyping.
When choosing the ideal metal for the mold, several factors must be considered, such as the thermoplastic melting point, production volume, and complexity of the part design. The mold material must have a higher melting point than the thermoplastic material used to avoid deformation or damage to the mold. Production volume is another critical consideration, impacting the tool’s lifespan and maintenance requirements.
In conclusion, selecting the appropriate mold material is integral to the success of an injection molding project. Choosing the right steel grade, tool steel or aluminum, based on factors such as production volume and thermoplastic melting point, can ensure the final product’s quality, production cost, and tooling life.
Mold Materials Used for Plastic Injection Molds
1. Steel: the most commonly used material for plastic injection molds due to its durability, resistance to wear and tear, and ability to withstand high temperatures and pressures.
2. Aluminum: a lighter and more cost-effective alternative to steel, commonly used for low-volume production runs or prototyping.
3. Copper alloys: used for specific applications where high thermal conductivity is required to help cool the mold during the injection process.
4. Nickel alloys: used for applications that require high strength and corrosion resistance.
5. Tool steels: a type of steel specifically designed for toolmaking and ideal for use in plastic injection molds.
6. Polymers: some molds are made of polymers, which are less durable than metals but are easier to work with and can be used for low-volume production runs or prototyping.
7. Ceramics: used for applications that require extreme heat resistance or where high levels of precision are required.
8. Composites: a combination of two or more materials, such as fibers and resins, that can be used to create molds that are lighter and more flexible than traditional metal molds.
Resin Selection
Choosing the right plastic resin is crucial in the injection molding process as it impacts the properties of the final plastic part. Several types of plastic resins are available, and each possesses unique characteristics that make them suitable for specific applications.
Commonly used plastic resins in injection molding include polypropylene, polyethylene, polycarbonate, ABS, PVC, and nylon. Polypropylene is widely used in the automotive industry for interior parts due to its toughness, chemical resistance, and low cost. Polyethylene, on the other hand, is preferred for bottle caps and packaging due to being lightweight, flexible, and moisture-resistant.
Polycarbonate is popular in the electronics industry for casing and covers as it provides high transparency and impact resistance. ABS is popular for consumer and household products as it offers high durability, strength, and heat resistance, ideal for applications such as toys and electronic housings. PVC is commonly used for plumbing parts because it has excellent chemical resistance and is flame-retardant.
Several properties must be assessed before choosing a specific plastic resin, including its tensile strength, toughness, chemical resistance, and melting point. The design requirements of the plastic part, such as complexity and wall thickness, must also be considered when selecting a resin to ensure optimal performance and desired final product.
Quality Requirements
Quality is of utmost importance in plastic injection molding, as it directly affects the performance and safety of the end product. It is critical to validate part quality before releasing it for use, especially in industries where safety is a top priority, such as medical, aerospace, and automotive.
One way to ensure consistent quality is by implementing testing and quality control procedures. These procedures can include dimensional inspections, performing material property assessments to analyze their physical and mechanical properties, and Statistical Process Control (SPC) to monitor production processes.
Part inspection is one of the most important aspects of quality control. It involves visual inspections, mechanical testing, and measuring dimensional accuracy. Material property assessments focus on identifying the strengths and limitations of specific materials, such as tensile strength, impact resistance, and stiffness. SPC monitors the production process, detecting and correcting issues before they affect the quality of the final product.
By implementing these testing methods and quality control procedures, manufacturers can consistently ensure that their products meet the required quality standards. In conclusion, quality requirements in plastic injection molding must prioritize validation of the part quality and ensure safety in critical industries, such as medical. Consistent quality can be achieved by implementing testing and quality control procedures such as dimensional inspections, material property assessments, and SPC.
Mold Manufacturer Location
When it comes to injection molding projects, the location of the mold manufacturer plays a significant role in the overall cost. Manufacturers that are located far away from the production site will result in higher shipping costs and longer delivery times, impacting the project’s timeline.
Selecting a reliable mold builder in the USA can help alleviate some of these concerns. Working with a local manufacturer means that communication will be more straightforward, without language barriers or time zone differences. The delivery times and shipping costs will also be significantly lower, reducing the impact on the project’s budget.
Furthermore, working with a reputable mold builder in the USA can provide other benefits, such as access to the latest technologies and materials and higher quality standards. This can lead to better-designed molds, longer-lasting tools, and ultimately higher-quality products.
Overall, the location of the mold manufacturer should be a key consideration in any injection molding project, and choosing a reliable mold builder in the USA could be an ideal choice to ensure project success while keeping costs under control.
Conclusion
In conclusion, plastic injection molding is an exciting and ever-evolving industry. Whether you’re a seasoned professional or just starting out, this comprehensive guide has given you the knowledge and tools to succeed.
Remember to always stay up-to-date with the latest technology and techniques, and never stop learning. You can create high-quality products that will make a difference in the world with dedication and hard work. Happy molding!
For Inquiries and questions about our services, call 303.806.5045 or visit: https://www.accelmachineshopdenver.com