What is Plastic Injection Molding
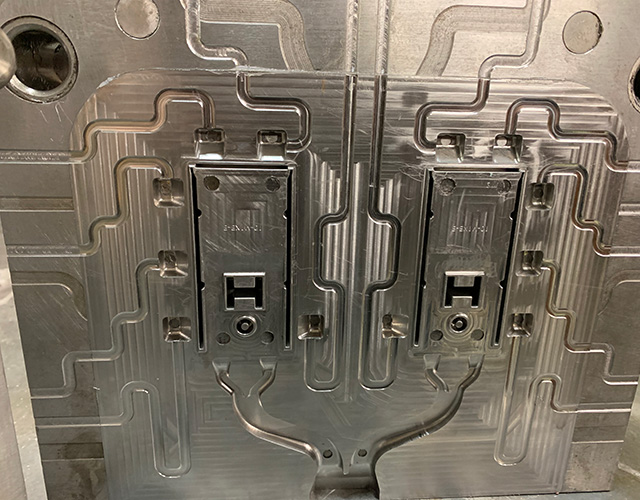
What exactly is plastic injection molding? How do you choose the right material for your part or product? What kind of quality control and testing standards exist?
Plastic injection molding is a manufacturing process used to produce plastic parts from raw materials. It involves heating molten plastic and injecting it into a steel or aluminum mold at high pressure. The shape of the part is determined by the shape of the mold, which can be custom-made for any product design.
Quality control measures are taken throughout the process to ensure that products meet design specifications while providing superior tensile strength and chemical resistance.
Plastic Injection Mold Building Process
This process is often automated and allows for high-volume production with accuracy and repeatability. Injection molding can produce parts in various sizes, shapes, and materials, making it an ideal choice for many industrial applications, such as automotive components.
Custom plastic injection molding is an important manufacturing process that can quickly produce high-quality components of various shapes and sizes with excellent detail and repeatability. As business owners increasingly look for ways to streamline their production processes, custom plastic injection molding services provided by companies like Accel Precision offer the ideal solution.
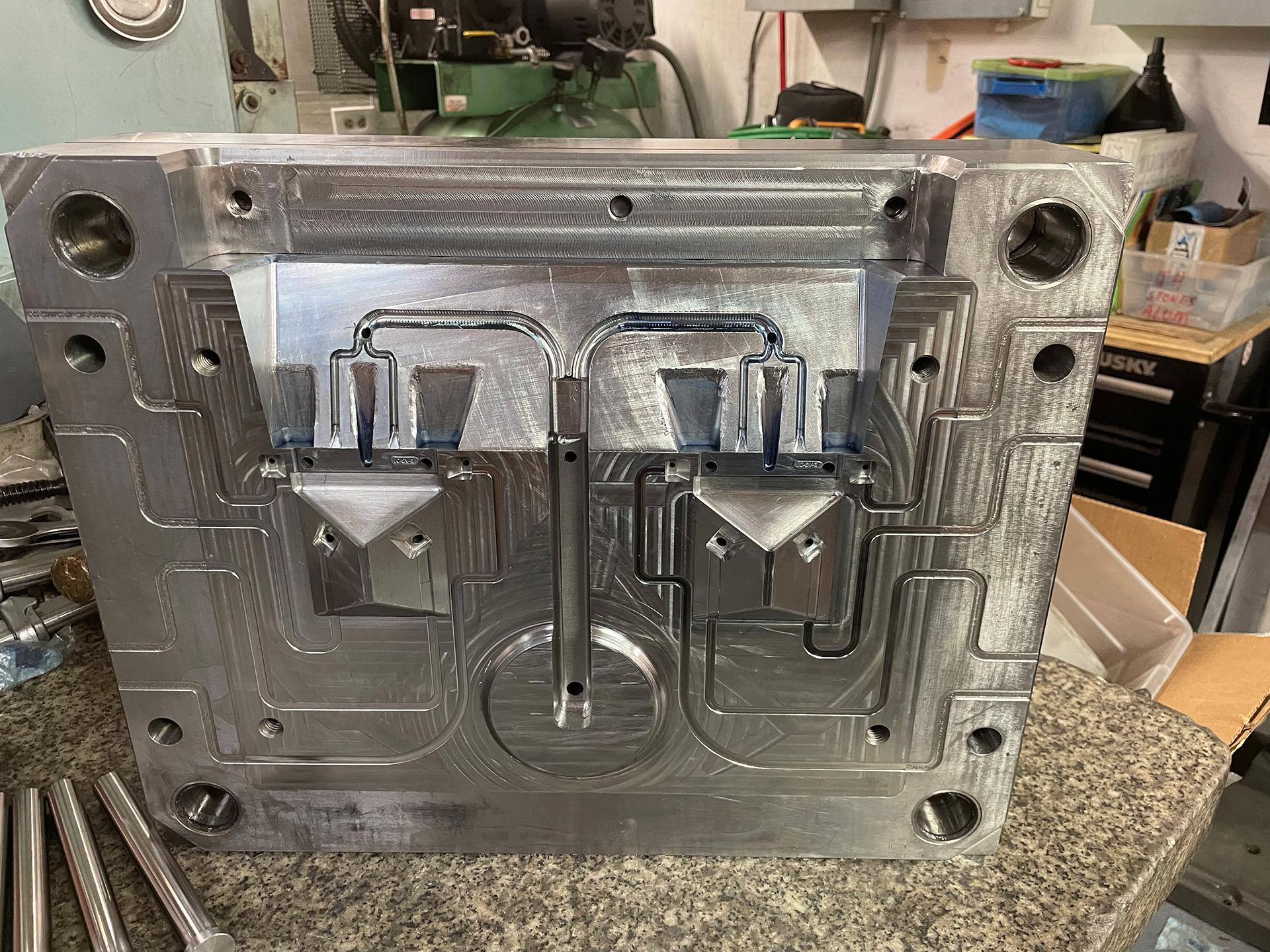
What are the advantages of injection molding?
The modern process of plastic injection molding is an incredibly versatile and efficient way to manufacture parts to create a wide variety of products. With the right equipment, it can also be less expensive for mass production runs than manufacturing with other materials such as metal. This process works by injecting molten plastic into a pre-made mold to produce objects in a fraction of the time of traditional methods.
The advantages that injection molding offers are numerous. Since the molds are made prior to production, overall turnaround times are usually very fast, requiring much less setup and leadtime than other processes in order to produce identical parts repeatedly and quickly. As
well, because this process produces parts up to high precision at large scale with great repeatability, tight tolerances can be held easily on thin walls and sharp corners for finished products with little variation between them.
How Long Does it Take to Make an Injection Mold Tool?
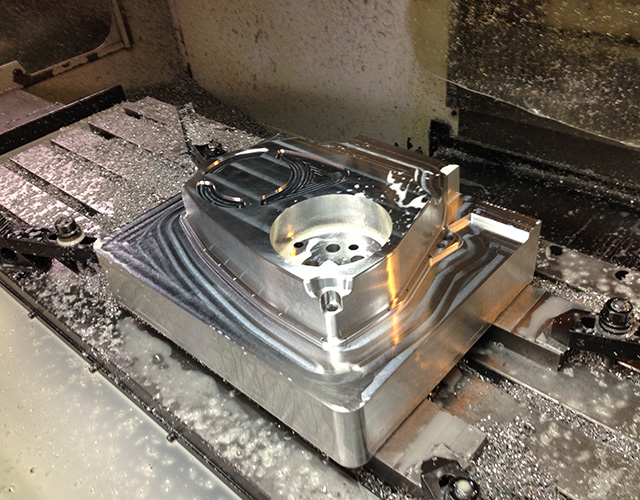
The time it takes to make an injection mold tool depends on the design’s complexity and any possible heat treatments that may be required. Depending on these factors, a plastic injection mold tool can be created in 4 to 6 weeks or longer, depending on how complicated the tool is.
Before this tool-making process can start, as much planning and preparation as possible must be completed beforehand. This includes creating detailed mock-ups of the final product, defining material and color requirements, deciding on production volumes, and ensuring space on the factory floor is reserved for production.
Getting all of these elements finalized before beginning the creation of the injection mold tool, it will help increase the chance of a successful project that requires minimal adjustments during production. Proper planning care allows for improved accuracy when machining and reduces preparation time.
Quality control measures are taken throughout the process to ensure that products meet design specifications while providing superior tensile strength and chemical resistance.
What Are The Main Cost Drivers for Plastic Injection Molding?
The main cost driver for plastic injection molding is the price of the Plastic Injection Mold tool. This is due to its large percentage of total order costs when producing small volumes. The initial cost is amortized for larger volumes and becomes less influential than other drivers.
This can be especially true with high-precision parts where additional time and complexity result in increased tool costs. Therefore, cost drivers such as material and cycle times become more significant in overall pricing as production volumes increase.
Material choice can greatly affect the total cost of plastic injection molding projects, as different resins will require different resources, tooling hours, and processing times.
Additionally, the cycle time required to inject a certain volume of product can have a major impact on the project’s overall cost. Reducing cycle time by utilizing advanced machinery or increasing machine efficiency can result in notable savings over longer production runs. However, it may come at an initial investment for new equipment or maintenance for existing machines.
Understanding these factors and working with reputable vendors is paramount to ensuring success within any plastics injection molding project.
Why Choose Accel Precision Machine and Mold for Plastic Injection Molding?
Accel Precision is the go-to choice for production tool-making and injection molding services. With 30 years of experience, we guarantee repeatable results when producing top-quality production mold tools. Our professional team of toolmakers strictly adheres to quality control standards to start with the finest raw materials in the industry, resulting in direct cost savings and improved efficiency throughout the production process.
Our focus on constant innovation and customer satisfaction has allowed us to stand out among competitors. We offer a wide range of services such as CAD/CAM development, mold design, engineering changes, CNC programming, 3D printing capabilities, quick turnaround times, and more, making us a complete solution for all your plastic injection molding requirements. In addition, our shipping capabilities enable delivery to any destination quickly and affordably.