What is a machine shop?
A Denver machine shop is a specialized facility where various tools, machinery, and skilled operators come together to create and fabricate various parts and components. These shops play a crucial role in manufacturing, offering the necessary expertise and equipment to carry out complex machining processes.
A machine shop is typically equipped with various machines, such as milling machines, drill presses, and 3D printers, to perform various manufacturing operations. From raw materials to finished products, a machine shop transforms ideas and designs into exact and accurate physical realities.
Whether it’s producing one-off prototypes or mass-producing parts, understanding the process of working with a machine shop is crucial for businesses needing manufacturing solutions.
Benefits of working with a quality machine shop
Working with a machine shop can benefit businesses needing custom tools and parts. These facilities have a wide range of manufacturing capabilities, allowing them to create high-quality products with precision and accuracy.
By utilizing the expertise of experienced operators, a machine shop can handle even the most complex machining processes, producing components that meet the specific requirements of a project.
One of the main advantages of collaborating with a machine shop is the efficient production time. With advanced machinery and skilled personnel, these shops have the ability to produce parts and tools at a faster pace, helping businesses meet tight deadlines.
Cost Effective Manufacturing
Machine shops often offer cost-effective pricing, allowing businesses to save on manufacturing process costs without compromising on quality.
Another major benefit of working with machine shops is the assurance of quality. These facilities typically have quality assurance protocols in place to ensure that all products meet the highest standards. From using state-of-the-art equipment to implementing thorough inspection processes, they can prioritize delivering top-notch results.
Effective communication is key when working with a machine shop. By clearly communicating project requirements and expectations, businesses can ensure that the final products align with their needs.
Efficient Prices and Production Processes
Collaborating closely with machine shop professionals can also help optimize manufacturing designs, resulting in more cost-effective and efficient production processes.
Working with a machine shop provides businesses with access to a wide range of manufacturing capabilities and experienced operators. A Machine shop’s efficient production time, cost-effective pricing, and quality assurance can greatly benefit businesses needing custom tools and parts.
Effective communication with the machine shop professionals is essential for the success of any project.
Finding the Right Machine Shop Operators
Finding the right standalone shop for your manufacturing process is crucial for the success of your project. With a wide range of machine shops available, it is important to carefully evaluate your options to ensure you choose the best fit.
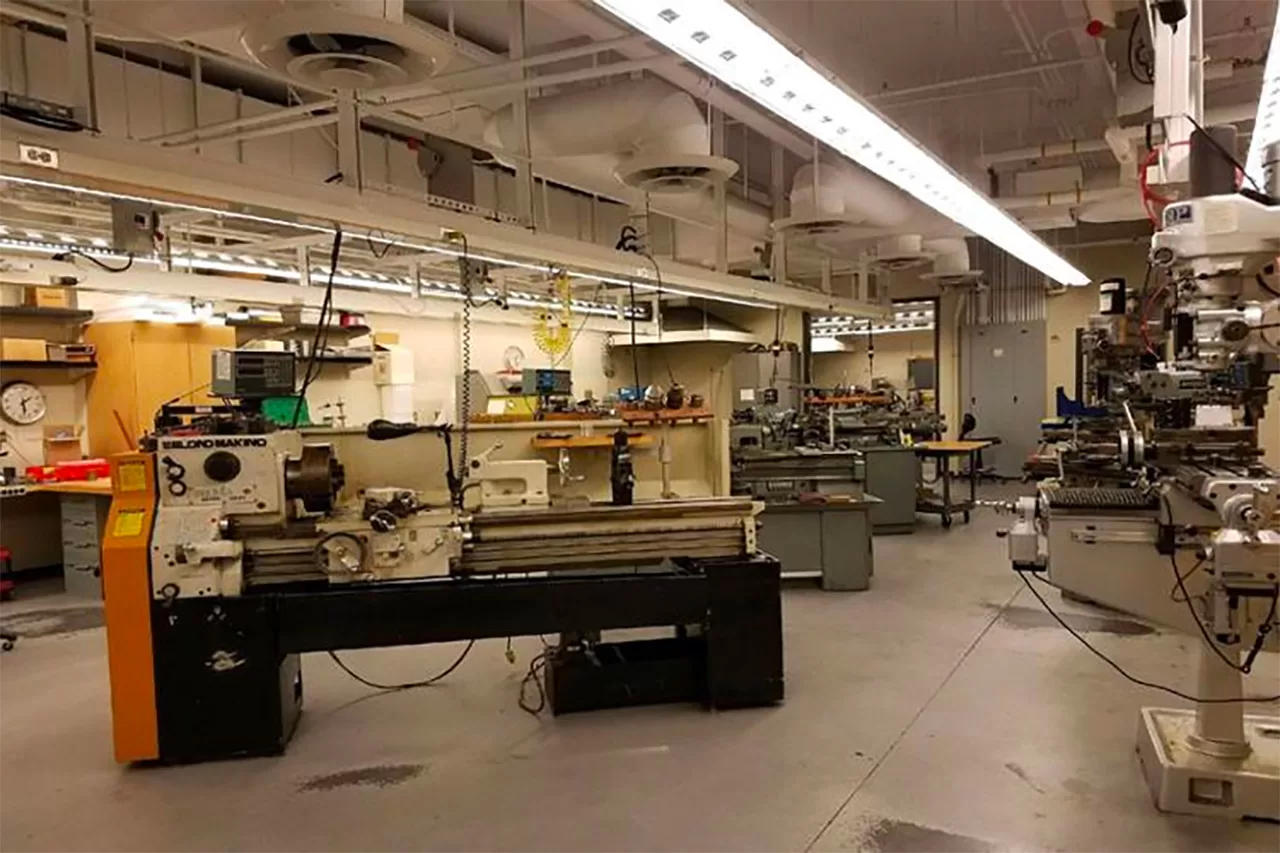
Identify your project requirements and understand the necessary machining processes and materials. This will help you narrow your search and find machine shops specializing in your desired manufacturing tasks.
Consider factors such as the shop’s experience, capabilities, and reputation for delivering high-quality products. It is also important to verify their adherence to safety standards and inquire about any certifications they may have.
Lastly, communication is key – choose a machine shop that values effective communication and is willing to collaborate closely with you throughout the manufacturing process. With the right machine shop by your side, you can ensure efficient production, superior quality, and successful project outcomes.
Setting Project Requirements and Goals
In the realm of machining services, it is essential to establish clear project requirements and goals to achieve desired outcomes efficiently and effectively.
Understanding the project’s specific needs and specifications helps identify the required materials and tolerances.
One of the most important aspects of setting project requirements is clearly defining the desired outcomes. This involves understanding the purpose and intended use of the final product, as well as any specific dimensions or design requirements.
By doing this, one can ensure that the machine shop understands the goals and can provide the necessary expertise to achieve them.
Identifying the right materials is another crucial step in setting project requirements. Each material has different properties and capabilities, and choosing the right one can impact factors such as durability, cost, and machining processes. Communicating the desired materials to the machine shop ensures that the chosen materials will meet the project requirements.
Lastly, specifying tolerances is vital in ensuring that the final product meets the required level of accuracy. Tolerances define the permissible deviations from the desired dimensions and shapes. Clearly communicating these tolerances to the machine shop allows them to utilize appropriate machining techniques and tools to achieve the desired level of precision.
Setting project requirements and goals is vital in working with a machine shop. By clearly defining project requirements, identifying necessary materials, and communicating specifications, one can ensure that the final product meets design, quality, and functionality expectations.
Researching Potential Machine Shops
One of the first steps is researching potential shops when embarking on a project requiring machining services. By finding the right shop, you can ensure that your project requirements are met and the final product is of the highest quality.
Start by conducting thorough research on machine shops in your area or online. Look for shops that specialize in your specific type of project. For example, if you need complex shapes or intricate designs, seek out machine shops that have experience working with similar projects.
Another important aspect to consider is the materials you will need for your project. Look for shops that have experience working with the materials you require. Whether it is metal alloys, plastics, or composite materials, finding a shop that has familiarity with your chosen materials is essential.
Shops With CNC Machining Centers
Evaluate the capabilities and equipment of the machine shops you are considering. Look for shops with various manufacturing capabilities and utilize modern machinery such as CNC machining centers and electrical discharge machining. A well-equipped shop will be better able to handle your project’s requirements.
It is also important to consider the experience and expertise of the machine shop. Look for reviews and customer feedback to gain insight into the shop’s reputation and the quality of its work. Positive reviews and testimonials can assure that the shop has a track record of delivering satisfactory results.
By researching potential machine shops specializing in your type of project, considering their experience working with materials, evaluating their capabilities and equipment, and looking at customer feedback, you can find a reliable and competent shop to fulfill your machining needs.
Making Final Selection
When it comes to selecting a CNC machine shop in China, making the final selection is a crucial step in ensuring your project’s success. To make an informed decision, there are several factors to consider and steps to take.
First and foremost, thoroughly evaluate the capabilities of each machine shop you are considering. Look for shops with various machining services and technologies to meet your project requirements. This includes assessing their equipment, such as milling machines and machining centers, to ensure they can handle your specific needs.
Next, consider the expertise and reputation of the machine shop. Look for testimonials or customer reviews to gauge the quality of their work and customer satisfaction. Additionally, inquire about their experience working on projects similar to yours, as this can indicate their level of proficiency in producing the desired results.
Pricing and terms are also important considerations. Compare the quotes of different machine shops, making sure to understand what is included in the price. Evaluate the shop’s pricing against the value they provide, considering factors such as turnaround time, quality assurance, and customer support.
Lastly, don’t forget to explore the shop’s communication and project management capabilities. Effective communication is crucial when collaborating on manufacturing tasks, so ensure the shop is responsive and has a clear process for project updates and feedback.
By carefully evaluating the capabilities, expertise, and reputation of CNC machine shops in China, and considering their pricing and terms, you can confidently make the final selection that will lead to a successful project outcome.
Negotiating a Machine Shops Pricing and Terms
Balancing a reasonable price and maintaining quality is important when negotiating pricing and terms with a machine shop. While it may be tempting to focus on low prices solely, this can often lead to compromised quality and subpar results.
Instead, aim to find a machine shop that offers a pricing model that is fair and profitable for both parties. This means considering factors beyond just the initial cost, such as turnaround time, quality assurance measures, and customer support. By evaluating these additional factors, you can ensure you get a competitive price while still receiving high-quality work.
During the negotiation process, be open to discussing your project requirements and desired outcomes. This allows the machine shop to provide a more accurate and tailored quote that aligns with your needs. Additionally, consider the shop’s profit margin and the value they provide in return for the price. Finding a mutually beneficial agreement is key to establishing a successful partnership.
Negotiating pricing and terms is about finding the right balance between cost and quality. By prioritizing both aspects and focusing on fair pricing and value, you can ensure a successful collaboration with a machine shop that meets your project requirements while delivering top-notch results.
Preparing for the Machine Shops Machining Process
Before working with a machine shop, preparing yourself and your project for the machining process is important. Start by gathering all the necessary information about your project requirements and desired outcomes. This includes specifications, dimensions, materials, and any other relevant details.
A clear understanding of your need will help you communicate effectively with the machine shop and eliminate misunderstandings. Additionally, consider the level of accuracy and complexity required for your project, as this will determine the type of machining techniques and equipment needed.
It is also essential to assess the timeframe and production volume required. This will help the machine shop determine if they have the capacity to meet your needs and deliver within the expected timeframes. Lastly, ensure you have all the necessary legal agreements, such as non-disclosure agreements, to protect your intellectual property.
By adequately preparing for the machining process, you can ensure a smooth and successful collaboration with the machine shop.
Understanding Your Project Needs and Specifications
When working with a shop, it is crucial to have a thorough understanding of your project needs and specifications. This ensures that your final product meets your requirements.
The first step is to define your project needs clearly. What is the purpose of your project? What are the desired outcomes? Understanding your project goals will help you communicate effectively with the machine shop and ensure they meet your expectations.
Next, identify the specific requirements of your project. This includes factors such as materials, tolerances, and specifications. Clearly communicating these requirements to the machine shop is essential to ensure that they have the necessary capabilities to complete the job accurately and efficiently.
When selecting materials for your project, consider factors such as strength, durability, and cost. Discuss these requirements with the machine shop to determine the best choice for your needs.
Tolerances are another critical factor to consider. Tolerances refer to the acceptable variations in dimensions that your project can have. Clearly define the tolerances that are acceptable for your project and communicate this information to the machine shop.
Lastly, provide the machine shop with detailed project specifications. This includes technical drawings, CAD files, or any other necessary documentation that outlines the specific details of your project.
By understanding and clearly communicating your project needs and specifications to the machine shop, you can ensure that your project is completed to your satisfaction, meeting all requirements and expectations.
Crafting an Effective Design Plan
An effective design plan is crucial when working with a machine shop. It involves considering the project requirements, materials, and tolerances and effectively communicating project specifications to ensure the desired final product.
To begin, it is essential to define the project’s purpose clearly. Understanding the intended outcome and objectives will guide the design process and enable effective communication with the machine shop. By knowing the precise goals, you can ensure that the final product aligns with your expectations.
Identifying the necessary materials is equally important. Consider factors such as strength, durability, and cost to determine which materials best suit your project requirements. Discussing these requirements with the machine shop will help determine the most suitable materials to achieve the desired results.
Tolerances, or acceptable variations in dimensions, are crucial in design plans. Clearly defining the tolerances that are acceptable for your project is vital. This information should be effectively communicated to the machine shop to ensure accurate and precise manufacturing.
Finally, providing detailed project specifications is crucial. Technical drawings, CAD files, or any other necessary documentation should clearly outline the specific details and requirements of the project. This ensures that the machine shop has a comprehensive understanding of your expectations.
By following these steps and effectively crafting a design plan that incorporates project requirements, materials and tolerances, and detailed specifications, you can ensure that the machine shop creates a final product that meets your desired specifications.
Selecting Appropriate Metals, Materials, and Tools
When embarking on a machining project, one of the crucial steps is selecting the appropriate materials and tools. The materials that can be machined are vast, ranging from metals like stainless steel, aluminum, brass, titanium, and copper to various plastics. Each material possesses unique properties, such as strength, durability, and conductivity, which must be considered based on the project requirements.
Milling Machines
To shape these materials effectively, a machine shop utilizes various tools. Common tools found in a machining shops environment include drill presses, manual machines, and rotary cutters. Drill presses are employed to create holes of various sizes while milling machines enable the cutting and shaping of materials. On the other hand, rotary cutters can trim and shape materials into complex shapes.
When selecting materials and tools, it is essential to consider factors such as project requirements, desired accuracy level, and the shapes’ complexity. Project requirements, including the desired strength and stability, help determine the most suitable materials.
The level of accuracy required also dictates the choice of tools, as machining materials can achieve varying degrees of precision. Additionally, the complexity of shapes needed for the project influences the selection of tools capable of handling intricate designs.
By carefully considering the project requirements, level of accuracy, and complexity of shapes, you can ensure the selection of appropriate materials and tools for your machining project. This thoughtful approach will provide you with the foundation to achieve your desired results efficiently and effectively.
Executing the Machining Process
The machining shops process involves several detailed steps to ensure accurate and efficient production. It begins with setting up the machine, which involves preparing it for operation by checking and adjusting various settings such as speed and feed rates.
Once the machine is set up, the next step is loading the workpiece onto the machine. The workpiece is securely clamped or held in place to prevent movement during cutting. Proper positioning and alignment of the workpiece are crucial to ensure precise machining.
The selection of the appropriate cutting tools is fundamental to the machining process. Different tools are chosen based on the machined material and the desired outcome. Factors such as cutting speed, tool geometry and coating influence the choice of cutting tools.
Operating the machine involves the actual execution of the machining process. This includes starting the machine, programming the necessary commands, and monitoring the process. The machine removes material gradually, creating the desired shape or form the design specifies.
Throughout the process, it is important to maintain a high level of accuracy and precision. Regular inspection and adjustments may be necessary to ensure the desired outcome. Effective communication between machine operators and shop supervisors is crucial to address any issues or modifications needed during the process.
By following these steps, machine operators can efficiently execute the machining process, producing high-quality parts that meet project requirements.
Safety Guidelines in Machine Shops
Safety practices are paramount in machine shops to prevent injuries and maintain a secure working environment. Following strict safety guidelines is crucial to safeguard the well-being of machine operators and other personnel in the workshop.
First and foremost, wearing appropriate clothing is essential. This includes wearing safety glasses to protect the eyes from any flying debris or sparks that may occur during the machining process. Additionally, operators should avoid wearing open-toed shoes instead of safety shoes that provide adequate protection.
Maintaining a Clean Shop
Maintaining a clean and organized shop is another vital safety practice. This involves keeping the floors free from any clutter, such as tools or materials, which can lead to tripping hazards. Furthermore, regular sweeping and cleaning of the shop effectively minimize dust buildup, preventing potential health risks and maintaining a safe environment.
Working With Hazardous Materials
Working with hazardous materials requires extra caution. Proper training and adherence to safety protocols are necessary to safely handle and store these materials. This includes using appropriate ventilation systems, correctly labeling containers, and following disposal procedures to prevent accidents and maintain a clean and safe working space.
In conclusion, machine shop safety is a top priority to ensure the well-being of everyone involved. Machine operators can work in a secure and hazard-free environment by adhering to safety guidelines, wearing appropriate clothing, and maintaining shop cleanliness.
Closing Out the Project with Your Machine Shop
Closing out a project with a machine shop is crucial in ensuring its successful completion. Properly closing out a project involves completing all necessary documentation and finalizing any outstanding details. This not only helps to ensure transparency and accountability but also sets the stage for future collaborations.
One of the essential steps in closing out a project is conducting a final inspection. This involves carefully examining the manufactured parts to ensure that they meet the project’s requirements and desired specifications. Any discrepancies or issues should be addressed and resolved before signing off on the project.
Reviewing Your Machine Shops Invoices
Reviewing and settling invoices is another crucial step in closing out a project with a machine shop. It is important to review the invoices carefully to ensure that all the services and materials used are accurately documented. Clear and open communication with the machine shop about discrepancies or concerns is vital for resolving outstanding financial matters.
Providing feedback is a valuable part of closing out a project. By sharing your experience and offering constructive feedback, you contribute to continuously improving the machine shop’s services. This feedback helps them understand areas of improvement and strengthens the relationship between you and the machine shop.
Closing out a project with a machine shop is not just a matter of wrapping things up. It is an opportunity to ensure all loose ends are tied, maintain transparency, and foster a mutually beneficial relationship for future collaborations. You can successfully close out your project with a machine shop through proper documentation, final inspections, reviewing invoices, and providing feedback.
Conclusion
In conclusion, selecting the right CNC machine shop is crucial for the success of any project. Working with a reputable machine shop brings numerous benefits, including access to advanced machining capabilities and experienced operators who can efficiently produce high-quality parts.
When choosing a machine shop, it is important to consider their range of manufacturing capabilities and experience in handling similar projects. A machine shop with a solid reputation in the industry is more likely to deliver accurate and precise results. Additionally, effective communication and collaboration throughout the machining process are essential. By clearly communicating project requirements and expectations, you can ensure that the machine shop understands your needs and can deliver satisfactory results.
Safety is a Priority
Adherence to safety practices is vital when working with a machine shop. It is important to prioritize safety by wearing appropriate safety gear, such as safety glasses and safety shoes. Moreover, closing out the project with the machine shop is essential to ensure satisfaction.
Conducting a final inspection, reviewing and settling invoices, and providing feedback contribute to a smooth project closure and further strengthen the relationship with the machine shop.
In summary, carefully selecting a machine shop, maintaining effective communication, prioritizing safety, and closing out the project collaboratively are all key factors in successfully working with a machine shop and achieving desired results.